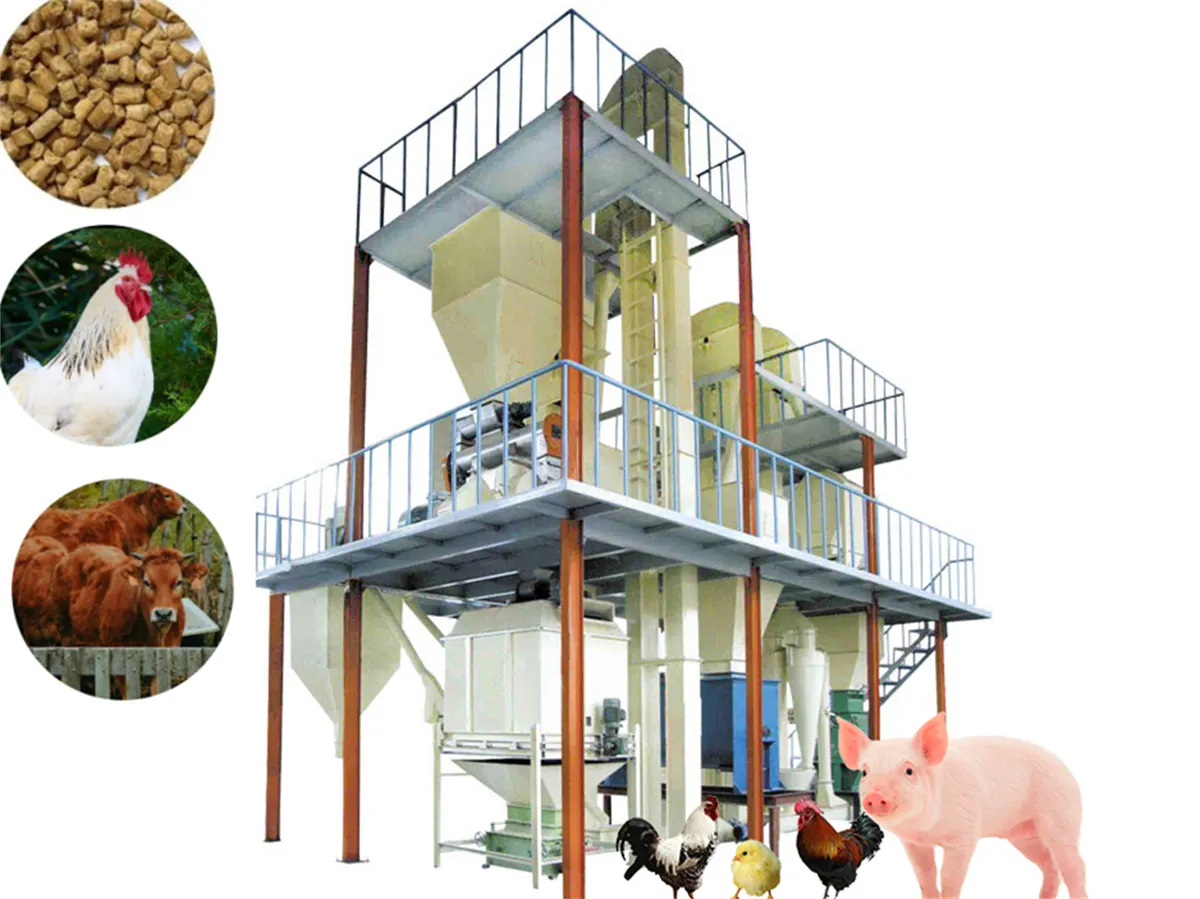
To establish a feed processing plant in rural areas, we must first conduct a thorough and detailed investigation, and then conduct economic analysis and technical demonstration on this basis. Only when the feeding industry needs it, has good economic benefits, has mastered advanced feed processing and preparation technology, and complies with the local regulations of "comprehensive planning, overall arrangement, adapting measures to local conditions, and reasonable layout" can we invest in building a factory.
Farmers who want to start a small feed processing factory should pay attention to the following points:
(1) Scientifically determine the scale of the factory. The scale of production is the basis for the design of the servo material processing plant. The scale of production should be determined based on the demand for feed in the supply area. The daily demand for feed can generally be calculated as 0.15 kilograms per day for laying hens and 1.75 kilograms per day for pigs. Then based on the total number of livestock and poultry raised in the supply area, the annual demand for feed can be calculated to determine the time for building the factory. Production scale. For example, an equipment with an annual output of 1,000 tons in a single shift can raise 20,000 laying hens or 1,500 pigs. According to the production capacity of the equipment and further considering the development plan of the local breeding industry or the current breeding scale, the tonnage of the equipment can be selected according to local conditions, thus scientifically determining the scale of the factory. (2) The correct choice of factory site should follow the principle of "nearby processing", and priority should be given to villages and towns with sufficient feed resources, developed animal husbandry and breeding industries, convenient transportation, guaranteed electricity, and markets, or where there are a concentration of specialized breeding households of a certain scale. village. If the feed mill is built near the grain depot or integrated with the grain depot, housing facilities and corresponding costs for raw grain storage can be omitted. Feed processing plants should not be built in places that are toxic, harmful, or polluted by pathogenic gases or dust, and should not be built near or downwind of livestock and poultry farms, pesticide factories, sewage disposal sites, etc.
(3) Carefully choose a pellet feed press. How to choose a pellet feed press is a concern of every farmer. When choosing a feed machine, you should choose products from regular, professional manufacturers, and shop around. Carefully select equipment. Before building a factory, the corresponding complete set of feed processing equipment should be selected based on the determined production scale. The following issues should be considered when selecting: the selection of the unit's process flow, whether the unit's process flow selection is reasonable or not, is closely related to the investment, energy consumption, use and maintenance convenience of equipment and workshops. For small servo material processing plants in rural areas, the equipment strives to be simple, so the process selection is required to be reasonable, simple and applicable. In rural areas, it is generally appropriate to choose the following three forms: ① Continuous proportional measurement - crushing - mixing; ② batch measurement - crushing - mixing; ③ crushing - batch measurement - mixing. The choice of unit measurement form includes volumetric measurement and gravimetric measurement. The advantage of volumetric measurement is that it saves labor, but it is not easy to change the formula; gravimetric measurement has higher accuracy and is more convenient to change the formula. Therefore, it is generally more accurate and convenient for small feed processing plants to use manual weighing. The selection of the unit is very important. The unit suitable for rural feed processing plants should have the following characteristics: ① The formula is easy to change, the proportion measurement is accurate, the mixing uniformity is good, and the feed particle size is adjustable. ②The unit has reasonable process flow, simple structure, convenient operation and maintenance, and the overall layout is compact and occupies a small area. ③ Low noise, less dust, and the unit must have safety control devices. ④ Low energy consumption, low price, and easy-to-purchase accessories. To sum up, for units with the same productivity, technical and economic indicators should be compared in terms of installed capacity, batching measurement method, power consumption, equipment selling price, required workshop area, etc., and a comprehensive analysis should be conducted to select the unit. required crew.
(4) Use the feed grinder correctly. The grinder should be fixed on the cement foundation for long-term operation. If the working location is frequently changed, the pulverizer and motor should be installed on a base made of angle iron. If the pulverizer is powered by a diesel engine, the power of the two should be matched, that is, the power of the diesel engine is slightly greater than the power of the pulverizer, and both The pulley grooves are consistent and the outer end faces of the pulleys are on the same plane. ②After installing the crusher, check the tightening condition of each fastener. If there is any looseness, tighten it. ③ Check whether the belt tightness is appropriate and whether the motor shaft and the pulverizer shaft are parallel. ④ Before starting the pulverizer, first turn the rotor by hand and check whether the claws, hammers and rotor are running flexibly and reliably, whether there is any collision in the casing, whether the rotation direction of the rotor is consistent with the direction indicated by the arrow on the machine, and whether the motor and pulverizer are Is the lubrication good? ⑤ Do not replace the pulley casually to prevent the crushing chamber from exploding due to too high a rotating speed, or too low a rotating speed affecting the work efficiency. ⑥ After starting up, the crusher should be idle for 2 to 3 minutes, and then start feeding after there are no abnormal phenomena. ⑦ Pay attention to the operation of the crusher at all times during work, and feed the material evenly to prevent clogging of the machine. Do not overload the machine for a long time. If any vibration, noise, excessive temperature of the bearings and body, or material spraying are found, stop the machine immediately for inspection and troubleshoot the problem before continuing to work. ⑧Crushed materials should be carefully inspected to prevent copper, iron, stones and other hard objects from entering the crushing chamber and causing accidents. ⑨ Operators should not wear gloves and should stand on the side of the crusher when feeding materials to prevent rebound debris from hurting the face. ⑩When it is clogged, it is strictly forbidden to use hands or wooden sticks to force feed or drag out feed.